AV Industrial Products: Quality
Quality Control
Here at AV Industrial Products Ltd we pride ourselves on providing high quality rubber engineering components to the industrial OEM market. We recognise the importance of quality control within the rubber engineering industry, and the high quality demands required of the OEM market. Having specialised in the manufacture and application of anti-vibration mounts and rubber engineering components for over 30 years we have an extensive in house testing facility to ensure full product compliance and the highest levels of quality (of both mechanical properties and material quality). Our expertise and reliability have earned us an outstanding reputation for supplying superior rubber components. That's why today we are proud to supply many of the UK, Europe and North America’s world leading 'household name' companies.
Our company is accredited to ISO9001 and ISO:140001, and follows a strict quality control regime for components manufactured, including testing and inspection to various quality standards including, ASTM D2000, ISO3302, ASTM D395 and BS6000. In addition, our range of marine mountings are design approved by Lloyds register of shipping, and our products are compliant with RoHS where applicable.
Our testing and quality control capabilities include mechanical testing of components, elastomers chemical compositions analysis, NDT testing, computer modelling and stress analysis. Below you will find further details on the company’s day-to-day testing facilities;
Compression & Tensile Testing
Within our laboratory our Quality engineers operate a number of Universal test machines for testing Compression stiffness and Tensile strength of rubber components, measuring such parameters as compression and shear stiffness (Kg/mm), bond strength, compression set, and damping.
We have facility to test up to 15000Kg, with the capability of testing both statically and dynamic cycling to simulate the expected working environment of the product. Testing can be ran for extended periods to perform accelerated life testing of products.
We are able to manufacture custom test jigs to test products in shear, as well as compression and tension, to ensure that all products are manufactured and controlled to acceptable working tolerances (typically +/- 20%)
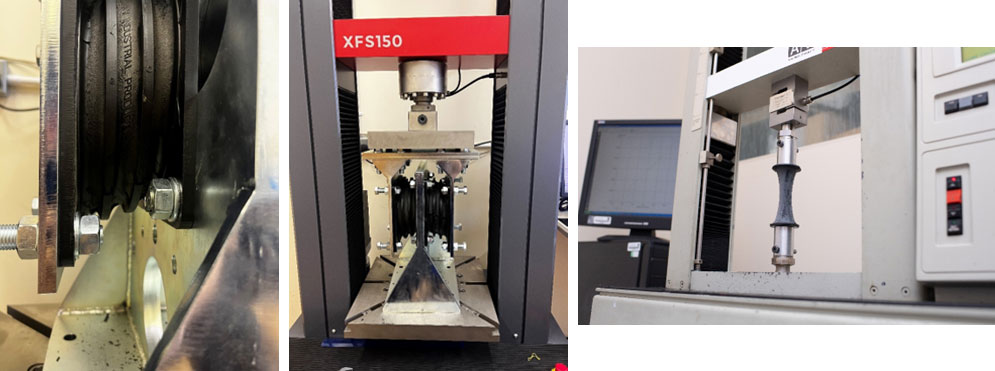
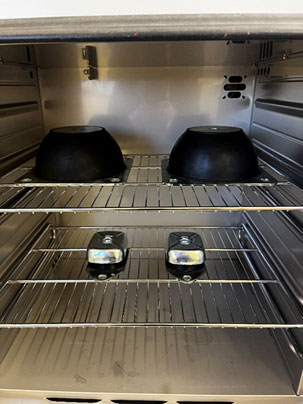
Temperature Chamber
The characteristics of rubber materials can be adversely affected by temperature, affecting mechanical properties such as stiffness, and in addition molecular changes (i.e. breakdown). It is therefore important that applications where extreme temperature is to be expected utilise correctly formulated rubber compounds. Our laboratory operates both a high temperature (upto 300 Deg C) and a low temperature chamber (down to -60 Deg C) which allows us to conduct a multitude of tests and analysis at extreme temperatures, including stiffness, tensile and hysteresis to measure the change in properties and ensure that the characteristics remain within acceptable limits.
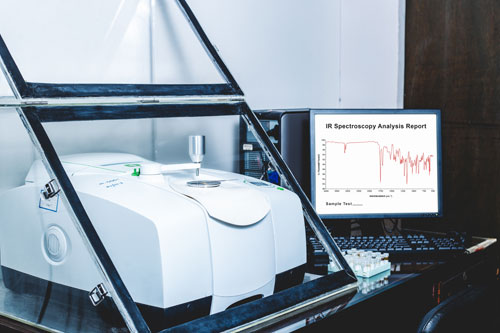
Polymer Analysis
Rubber formulation is a complex process of mixing numerous ingredients to create a rubber compound, including the raw polymer, reinforcing fillers such are carbon black, curatives, and various other chemicals and additives to provide the required properties.
However, most rubber compounds appear identical in appearance and the user can have difficulty identifying the materials, formulation and quality.
As part of our product development process, we have capability to analysis and measure various polymer characteristics to ensure that our products meet your quality requirements and offer the required mechanical properties, whether it be material type, UV & Ozone resistance or dynamic characteristics.
We can conduct a range of rubber analysis including material type (chemical reaction), specific gravity, oil and fuel swell rates, and reverse engineering of formulations (i.e. TLC, TGA and FTIR analysis)
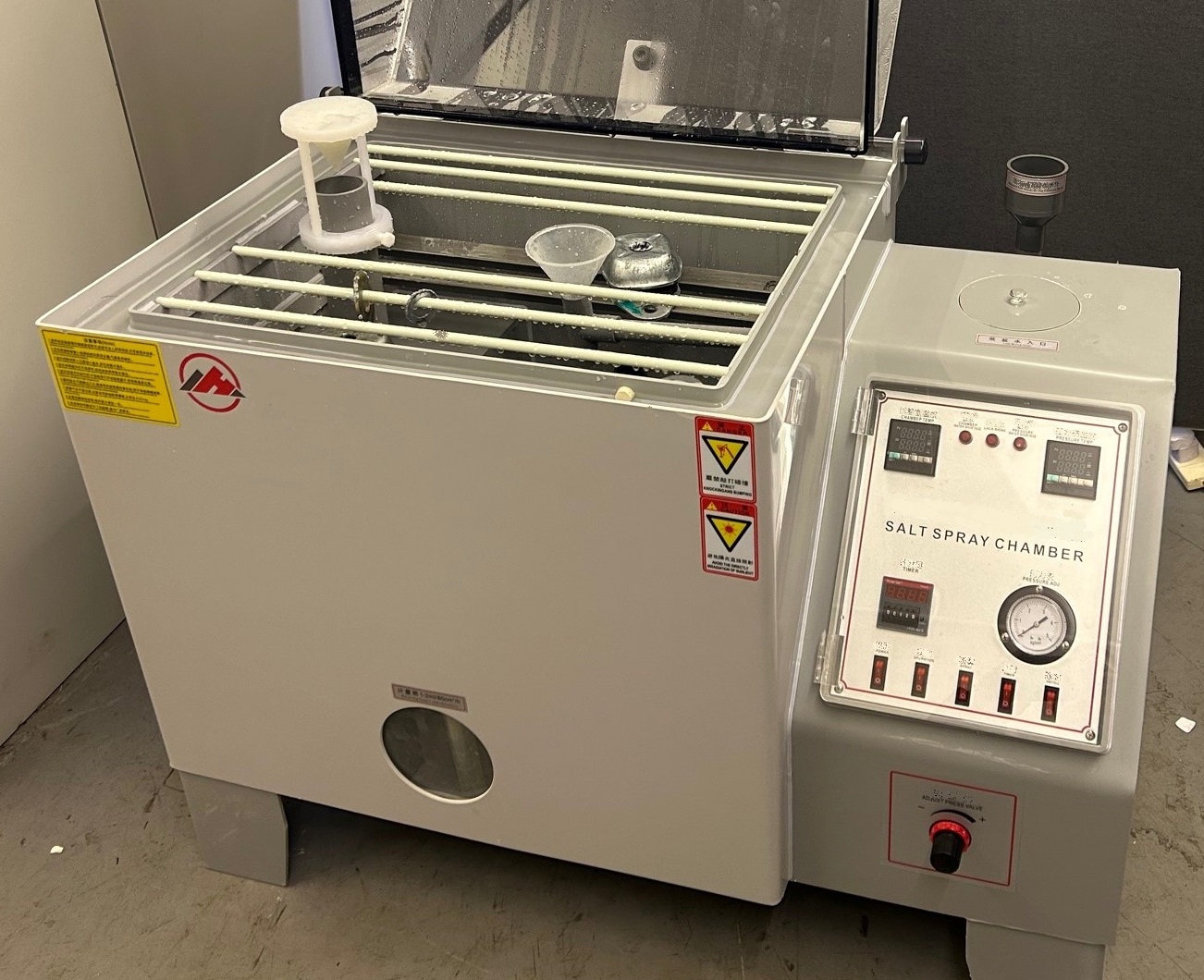
Salt Spray Chamber
We utilise a Salt Spray Chamber at to our testing facilities, allowing us to conduct corrosion testing on a wide range of components, including rubber-to-metal bonded components and anti-vibration mountings.
The salt spray chamber is primarily utilized to measure the corrosion resistance of various materials, particularly steel components with protective finishes such as Zinc Plating and Painted metal surfaces. One of the typical tests conducted is known as a neutral salt spray test (NSS).
By subjecting our components to rigorous corrosion testing, we ensure that they meet the highest standards of durability and performance even in harsh environments. This testing helps us guarantee the longevity and reliability of our products, providing our customers with peace of mind.
Additional Quality Control Testing
- Specific Gravity of polymer
- Rubber Hardness (Shore A)
- Compression Set
- Permanent Set
- Hysteresis
- Fuel and Oil Contamination (Swell rates)
- TLC, TGA & FTIR material analysis
- PPAP / ISIR
It should be noted that rubber products should be stored in accordance to ISO2230. Our own storage guidance can be found here – Storage of Rubber Products
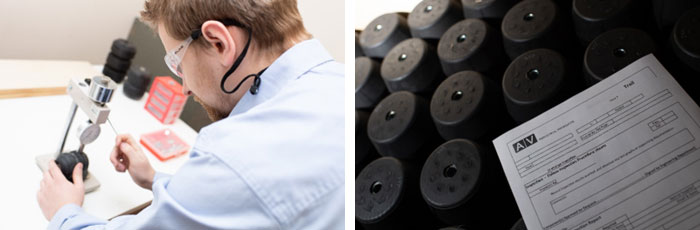