Electric Vehicles
The Role of Anti-Vibration Mountings in Electric Vehicles
As the automotive and off-highway industries transition from internal combustion engines (ICE) to electric motors (EM), effective noise, vibration, and harshness (NVH) control remains essential. While EVs operate more quietly, the absence of engine noise makes other sounds - such as road and auxiliary component vibrations - more noticeable, requiring refined vibration isolation strategies.
Electric motors also deliver instant torque, introducing rapid load changes that can affect the chassis and drivetrain. This necessitates anti-vibration mountings designed to handle these dynamic forces while maintaining vehicle stability and comfort. Traditional ICE mounts may not always be suitable, leading to the development of specialised solutions using advanced rubber compounds and viscoelastic materials for optimal damping.
Beyond the powertrain, components like battery packs, inverters, and cooling systems generate vibrations that must be managed for durability and performance. Effective anti-vibration solutions enhance ride quality, extend component life, and contribute to the overall refinement of electric vehicles. As EV adoption grows, ongoing innovation in mounting technology will play a key role in optimising NVH performance.
Anti-vibration mountings play a crucial role in several key areas of electric vehicles (EVs), including:
Powertrain Mounts – Supporting electric motors and inverters while managing torque and vibration.
Suspension Mounts – Absorbing road-induced vibrations in heavier EVs.
Battery Isolation Systems – Reducing dynamic loading and extending battery life.
Battery Cell Mounts – Protecting individual battery cells from excessive vibration and thermal expansion effects.
Cabin Mounts – Enhancing operator comfort by minimising NVH.
Ancillary Equipment Mounts – Isolating components like cooling systems, inverters, and power electronics from unwanted vibrations.
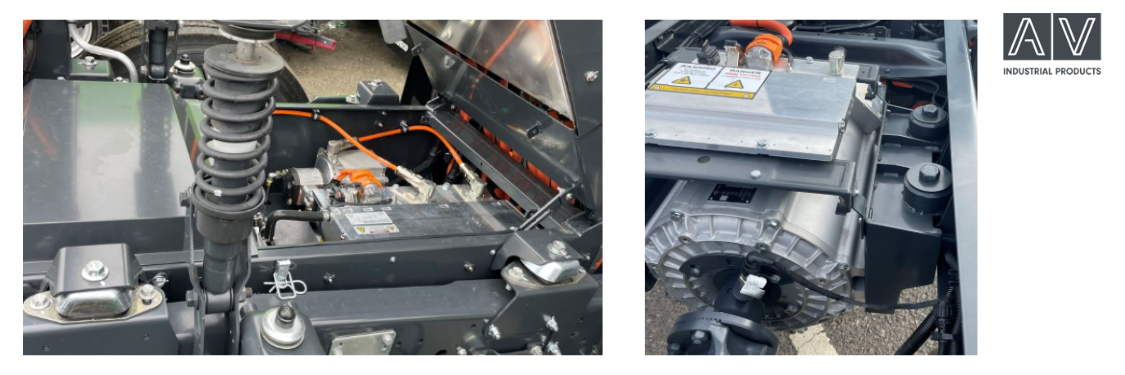
Key Technical Considerations for EV Anti-Vibration Mounts
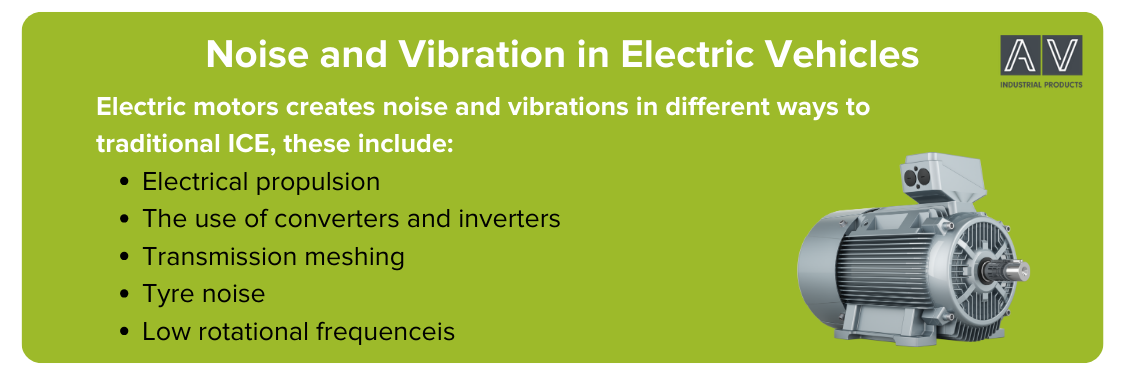
1. Vibration Spectrum of Electric Motors vs. Internal Combustion Engines
Unlike ICEs, which generate low-frequency vibrations (typically between 20-200 Hz) due to cyclic combustion events, electric motors produce higher-frequency vibrations, often exceeding 500 Hz, caused by electromagnetic forces, inverter switching, and gear meshing. This requires mounts designed to dampen high-frequency resonances more effectively.
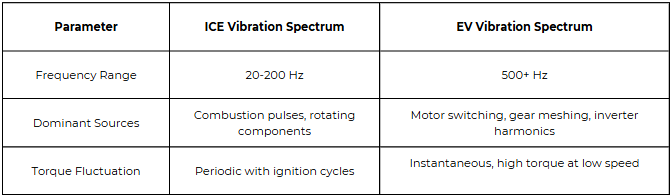
2. Torque Considerations in EVs
Electric motors deliver instant torque, which means the mounts must handle sudden, high-force loads. This results in greater bi-axial load transfer (side-to-side and frontto-back movement), requiring mounts with:
- Higher shear and compressive strength to withstand rapid torque surges.
- Optimised damping characteristics to prevent excessive movement.
- Torsional flexibility to accommodate load shifts.
3. Material Considerations for EV Mounts
Traditionally, natural rubber has been the preferred material for anti-vibration mounts due to its excellent damping properties and durability. Whilst this remains the case for EV applications, additional materials can offer other benefits:
- Natural Rubber (NR): Excellent resilience and isolation properties.
- Silicone Rubber (SI): Withstands high temperatures and offers better electrical insulation.
- EPDM (EPDM): Superior resistance to weathering and ozone exposure.
- Chloroprene Rubber (CR): Improved resistance to oils and chemicals found in EV cooling systems.
Typical Vibration Frequencies in EVs
Electric motors, inverters, and power electronics introduce new vibration profiles. Below is a comparison of typical vibration frequencies in EV components:
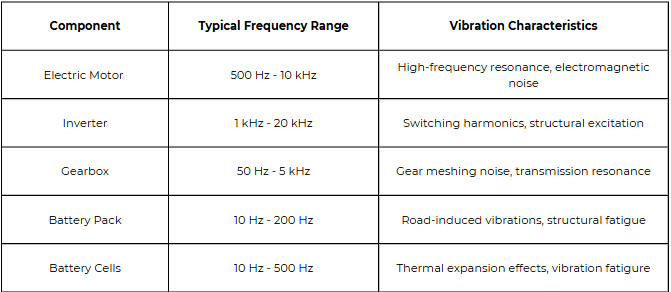
Three-phase electric motors are often the preferred choice for construction and industrial vehicles due to their high efficiency, durability, and superior torque characteristics. Unlike single-phase motors, three-phase motors provide continuous and balanced power delivery, reducing vibrations and ensuring smoother operation. Their high starting torque makes them ideal for heavy-duty applications, such as electric excavators, loaders, and dump trucks, where significant force is required to move heavy loads.
The graph illustrates and example of the key harmonic frequencies generated by a 3- phase, 6-pole electric motor running at 1000 RPM. The mechanical rotation frequency is 16.67 Hz, while the fundamental electrical frequency is 50 Hz, as determined by the motor's pole count. Electrical harmonics appear at multiples of the fundamental frequency, with the 5th (250 Hz), 7th (350 Hz), 11th (550 Hz), and 13th (650 Hz) harmonics being prominent.
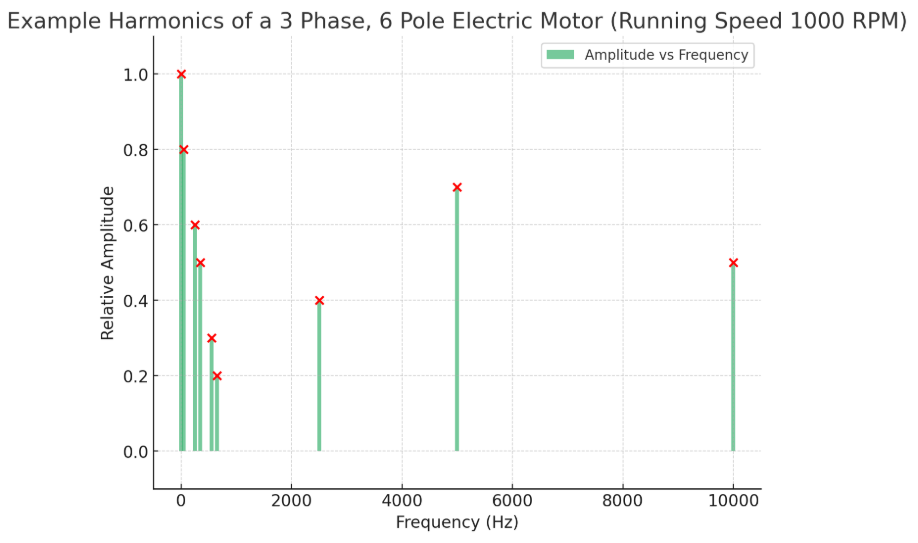
Addressing NVH Challenges in EVs with Anti-Vibration Mountings
To minimise noise and vibration, AV Industrial Products Ltd provides industry-specific solutions that address these challenges:
Custom Engineered Mounts: Optimized for EV torque response and highfrequency damping.
Battery Isolation Systems: Protecting battery packs and individual cells from road vibrations and extending lifespan.
Cabin Mounting Solutions: Ensuring operator comfort with precision-engineered NVH control.
Durable Materials: Using rubber compounds optimized for EV conditions, including temperature extremes and high torque loads.
Partnering with AV Industrial Products for EV Solutions
With decades of experience in vibration isolation for off-highway and automotive industries, AV Industrial Products Ltd understands the unique demands of electric vehicle applications. We offer tailored solutions designed to:
- Minimise noise, vibration, and harshness (NVH).
- Extend component lifespan and reliability.
- Enhance operator safety and comfort.
- Improve vehicle durability and reduce downtime.
- Support environmental and regulatory compliance.
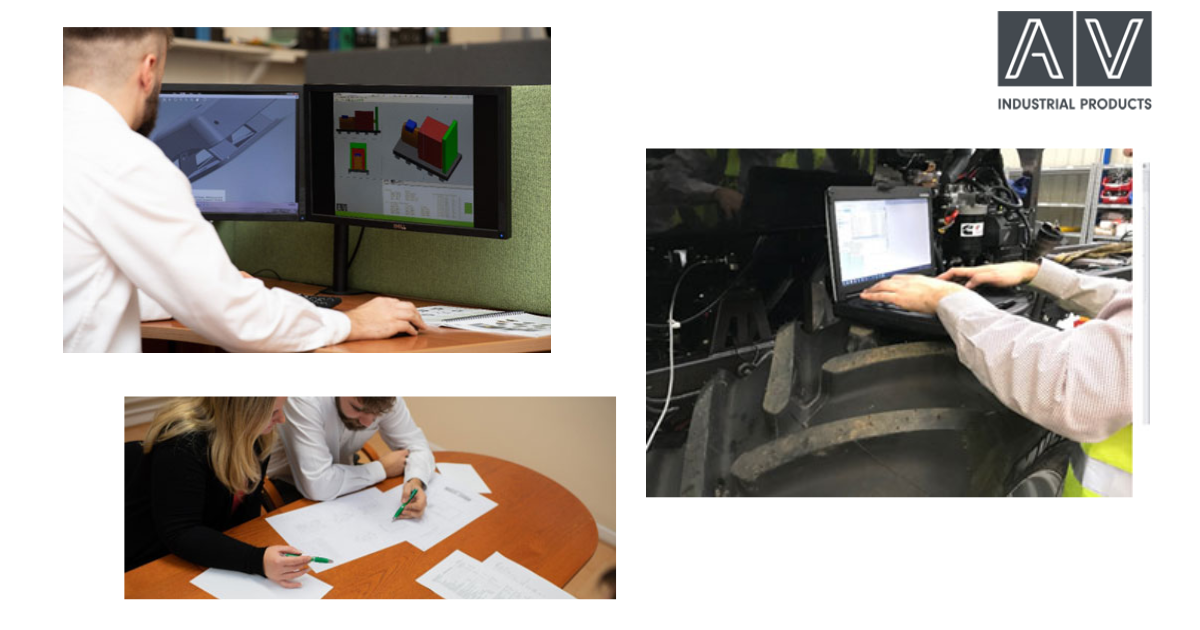
As the industry moves towards electrification, selecting the right anti-vibration solutions will be critical in ensuring performance, efficiency, and longevity in electric vehicle fleets. Contact AV Industrial Products Ltd today to discuss how we can support your EV vibration control needs.
AV Industrial Products Ltd
www.avindustrialproducts.co.uk
engineering@avindustrialproducts.co.uk
+44 (0)116 2461261