Rubber is everywhere. Whether it’s the tires on your car, rubber matting in your garage, or engine mountings on a tractor. It remains one of the most common materials for many applications and comes in many types and formulations.
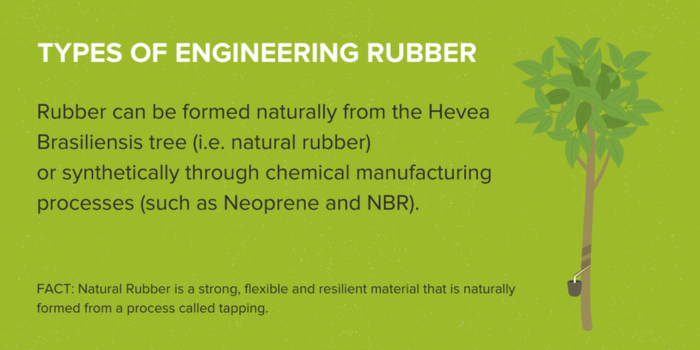
Rubber, as a raw material, can be formed naturally from the Hevea Brasiliensis tree (i.e. natural rubber) or synthetically through chemical manufacturing processes (such as Neoprene and NBR).
Rubber has been used for thousands of years and has proven to be a solid choice for many products in both a domestic and industrial setting.
However, it is important that the right rubber material and formulation for your specific application are selected in order to achieve the required characteristics and lifespan.
What is Rubber and why is it so Flexible?
Natural Rubber is a strong, flexible and resilient material that is naturally formed from a process called tapping. These natural rubbers are extensively used in many applications such as tires and anti vibration mounts, however, industrial demand for materials similar to natural rubber began to surpass natural rubber supply by the end of the first world war. This demand led to the creation of synthetic rubber, manufactured by chemical means, as an alternative to natural rubber.
So, why is rubber so flexible?..... During unstrained conditions the molecules of rubber are irregularly coiled together. When force is applied to these molecules they straighten out in the direction they are being pulled. As soon as the force is released,the molecules return to their normal coiled up arrangement. This molecular structure creates the flexible nature of rubber. In addition, during the vulcanisation process, where various chemicals and additives are added to the raw rubber, the molecular structure creates bonds and cross links which further increase the strength of the rubber and its desire to return to its original “coiled” molecular structure. - i.e. creating resilience.
What’s the Difference Between Rubber and Latex?
Natural Rubber is a material made from Latex. Latex is collected from the Hevea Brasiliensis tree, as a milky white sap from the bark - through a process called tapping. The sap later becomes rubber with the addition of formic acid and drying processes.
What is the Temperature Range of Rubber?
The temperature range of rubber depends on the rubber type and its formulation. However, broadly speaking natural rubber will operate between -30° and +75°C without breakdown. Synthetic rubber materials can considerably improve on this, with some exotic compounds being able to accommodate in excess of +250°C, however there will often be a compromise on other mechanical properties. During low temperatures rubber can crystallise and become brittle. These differing properties affect how we use rubber across different applications.
The Most Common Types of Rubber and Their Uses
Let’s run through the most common types of rubber and their typical uses.
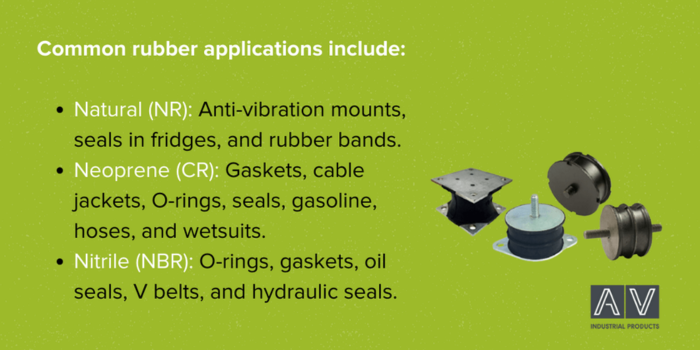
Natural rubber (NR)
Natural rubber, as with most, is elastic and has a resistance to abrasion, extreme temperatures, water swell, friction and can withstand repetitive forces in different directions. Natural rubber is harvested in the form of latex. It is then refined into rubber ready for commercial processing.
The latex is mixed with formic acid and then gets processed into dry forms ready to supply to the manufacturing plants. In order to create an engineering rubber the dry forms will then be compounded with other additives such as carbon black and sulphur.
Chloroprene rubber (CR)
Chloroprene rubber (sold under the brand name Neoprene) is a durable rubber that closely emulates the properties of Natural rubber, with the additional benefits of being resistant to certain fuels and oils and having a higher temperature rating (typically upto 110 degrees C). It is generally 30-40% more expensive than Natural rubber, and has a slightly lower resilience. It should be noted that there are a wide range of grades of Neoprene, suitable for various different applications. Selecting the incorrect grade can have significant impacts.
Nitrile rubber (NBR)
Nitrile Rubber–also known as NBR rubber or nitrile butadiene rubber has excellent oil resistance properties, mechanical and chemical properties, and also has a slightly improved temperature resistance compared to Natural rubber. Resilience is lower than Natural Rubber. Typically used for Seals and Gaskets.
Silicone rubber
Another common, but different, kind of rubber is silicone rubber. This synthetic rubber is recognised for its biocompatibility and heat resistance properties. It can be formulated to be resistant to fire, ozone, and ultraviolet radiation - depending on formulation. It also offers extremely high temperature resistance, typically in excess of 200 degrees C. However, the material has lower tensile strength compared to natural rubber and is approximately 300-400% higher in price. Silicone rubber generally is not reactive, making it great for products that demand biocompatibility, such as products for the medical and food industry.
Butyl rubber
Butyl rubber is a synthetic polymer manufactured by combining isobutylene and isoprene. It was one of the first rubber to be synthesised, back in 1937. It has excellent shock absorption characteristics and also benefits from low moisture and gas permeability, and is used in many commercial applications. Within the Anti Vibration industry it can be found in anti vibration mountings for 3 cylinder engines to control the high amplitude (movement) due to out of balance forces.
Type of Rubber: | Natural or synthetic: | Common Uses: |
Natural (NR) | Natural | Anti Vibration Mounts, Seals in fridges and automation, rubber bands |
Neoprene (CR) | Synthetic | Gaskets, cable jackets, O-rings, seals, gasoline, hoses, wetsuits, and orthopaedic braces, and anti vibration mounts |
Nitrile (NBR) | Synthetic | O-rings, gaskets, oil seals, V belts, hydraulic seals |
Silicone | Synthetic | Food products, apparel, sportswear, footwear, electronics, repair and hardware, and high temperature industrial application |
Butyl | Synthetic | Shock absorption (energy absorption) applications, Wire and cable insulation, steam hoses, mechanical goods, adhesives. |
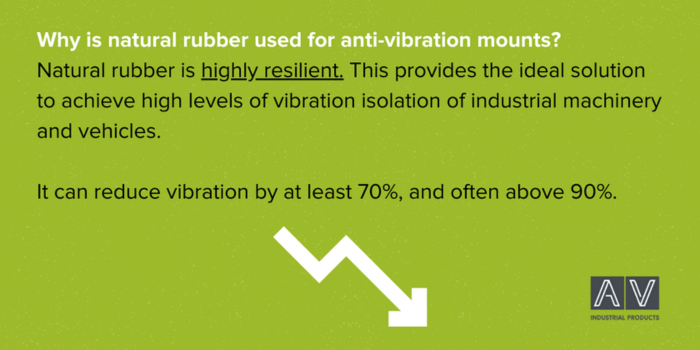
Why is Natural Rubber Used for Anti-Vibration Mounts?
Natural Rubber is the material of choice for most anti-vibration mounts, offering many preferable advantages, both technically and commercially.
Natural rubber is highly resilient in nature. Resilience is a measure of energy required to deform a piece of rubber, against the amount of energy returned during the rebound back to its original shape. The inverse of Resilience is “Hysteresis”, which is the percentage of energy lost during deformation. Hysteresis results from molecular friction inside the rubber which creates heat build-up. (i.e.energy is lost due to heat and not returned).
This high resilience property provides the ideal solution to achieve high levels of vibration isolation of industrial machinery and vehicles. Depending on application and anti vibration mounting type, it can be expected that vibration will be reduced by at least 70%, and often above 90%.
Other Uses of Rubber
In vehicle suspension, natural rubber bushes are used. This is because they have high tensile strength and the high resilience properties are ideal for noise and vibration suppression. Rubber bushings help to isolate sound and serve as boundaries between components in close proximity. In addition rubber bushes allow controlled movement of the vehicle's suspension system and chassis components.
At AV Industrial Products, we specialise in the manufacturing of anti-vibration mounts and have a team of Application and Design engineers that can advise on the best solutions for your application. We have a long-standing and high-level technical expertise and knowledge, remaining a market leader within the vibration control and rubber engineering industry.